礦渣烘干采用順流式回轉烘干機,規格∮2.4mx25m,自2003年11月投產以來烘干機雖能達到設計能力,但烘干機簡體和沸騰爐接口處仍存在一些問題,運行狀況不夠理想。在2005年大修時,對該部位進行了綜合改造,取得了較為理想的效果。
1、存在的問題
烘干機與沸騰爐接口處的結構如圖1所示。
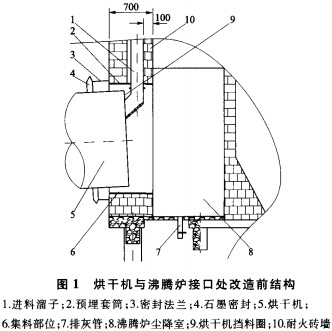
1)在烘干機與沸騰爐接口處,筒體與預埋套筒及密封法蘭之間積料,造成簡體磨損嚴重,被迫將石墨密封下部拆除卸料,導致冷風進入,降低了沸騰爐的熱工效率。
2)進料溜子使用壽命很短,一般2~3個月左右需要更換,且安裝相當困難。
3)預埋套筒頂部燒蝕塌陷,沸騰爐端墻出現裂縫下沉,墻體的重力落到筒體端部,阻礙筒體運轉,
4)沸騰爐塵降室沒有設計擋火墻,造成熱風直接燒蝕筒體、預埋套筒及進料溜子,致使烘干機擋料圈燒蝕變形,開焊斷裂。
5)沸騰爐塵降室沒有設計集灰斗,造成進入塵降室的灰塵及飛濺物料不能及時排走,堆積到一定程度時,才能一部分從中間∮200mm的排灰管排出,一部分存留在筒體與預埋套筒之間,一部分從密封法蘭底部擠出。
2、解決方案及措施
2005年1月大修時進行的改造如圖2所示。
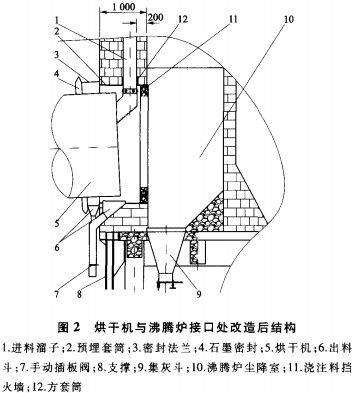
1)擴大沸騰爐端墻厚度,由原設計700mm向外擴到1000mm,基礎采用工字鋼支架。下料溜子向烘干機方向平移100mm,增大了下料溜子穿過預埋套筒后面的空間。在預埋套筒上下料溜子穿過的部位,采用20mm厚板材制作的方套筒與預埋套筒進行焊接,增強了預埋套筒頂部的整體強度,下料溜子從方套筒中間穿過進入烘干機。預埋套筒前端(靠近烘干機端)采用拱頂磚砌碹,方套筒兩側拱頂磚與前后碹墻咬和砌筑發碹,解決了端墻全部重力壓在預埋套筒上的問題。
2)在預埋套筒底部和密封法蘭處增加排灰裝置,及時將該處積料排出,解決了筒體磨損的問題。將沸騰爐塵降室樓板打通,加裝集灰斗并在灰斗內表面打上80mm厚的澆注料,防止灰斗灼燒變形。將原設計的石墨密封恢復,以減少冷風進入。
3)為方便安裝和檢修,入料溜子由法蘭連接改為螺栓懸掛方式,并在溜子背面打上澆注料,防止高溫空氣的直接燒蝕,延長了入料溜子使用壽命。溜子規格由300mmx400mm加大到500mmx450mm,溜子鋼板厚度由8mm增大到16mm。
4)由于烘干機簡體與沸騰爐端墻接口部分磨損嚴重,擋料圈開焊嚴重變形,為防止擋料圈的灼燒,在預埋套筒內部砌筑內徑為∮1800mm的環行澆注料擋火墻,一方面保護擋料圈,另一方面集中進入烘干機的熱空氣,提高烘干機的烘干效率。
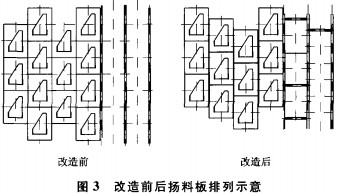
5)另外,對弧型揚料板與簡體的連接方式也進行了改進(見圖3),由環狀焊接改為框式焊接,降低了礦渣顆粒進入揚料板與筒體內部環行空間內長距離的磨刷。同時改變弧型揚料板的安裝布置方式,由交錯半塊揚料板的布置,改為交錯1/3塊揚料板的布置,使成為螺旋狀布料,大大改善了礦渣在烘干機內形成的料幕,增加了物料的熱交換空間,提高了烘干機的熱工效率。
3、經濟效益
改造后近兩個月的運行數據和改造前的對比見表1,可見,改造后烘干機的運行狀況得到了改善。